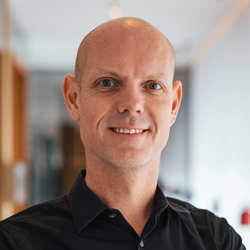
Rex Clements
CEO, Centrient Pharmaceuticals
Innovative pharmaceutical companies that make antibiotics are taking steps to reduce the negative potential consequences of AMR pollution in their manufacturing processes.
Antimicrobial resistance (AMR) is often referred to in the future tense as if it’s a brewing healthcare crisis. We have to get real, insists Rex Clements, CEO of antibiotic manufacturer, Centrient Pharmaceuticals. AMR — which makes infections harder or even impossible to treat with antibiotics — is an urgent crisis of the here and now.
Ongoing AMR global health threat
The Global Research on Antimicrobial Resistance (GRAM) Project predicts that antimicrobial resistance will cause 39 million deaths — that’s three deaths per minute — between 2025 and 2050. “Effective antibiotics are the foundational medicines of any healthcare system,” says Clements. “Yet, we increasingly see bacteria and other microbes develop resistance to the available medicines. So, according to the World Health Organization (WHO), AMR is considered a top global health threat right now.”
How antibiotics manufacturing can contribute to AMR
There are various reasons why AMR has become a clear and present danger. It’s well-reported that its main drivers are the overuse or misuse of antibiotics and the lack of new antibiotics coming onto the market. “Yet, there’s a third driver which is of huge concern to us as antibiotics manufacturers,” says Clements. “This happens when antibiotics are released into the environment from waste products in the manufacturing process.” Essentially, if a high burden of active antimicrobials is present in pharma factory wastewater — and that wastewater is then released into waterways — it can contribute to AMR pollution.
Making pharmaceutical manufacturing responsible and sustainable
Pharma companies therefore need to adopt a rigidly controlled and sustainable manufacturing process, of the type practised by Centrient Pharmaceuticals. Clements admits that this responsible approach is personal. “I have three children,” he says. “Frankly, I want them to grow up in a world where antibiotics work. So, I have absolutely no interest in running a company that contributes to AMR. We’re one of the first companies globally to focus on pharma manufacturing in a sustainable way.”
If practices generate AMR, it will
reduce the effectiveness of our antibiotics.
In 2000, the company developed its enzymatic manufacturing process. It requires less energy and water, and it avoids the use of harmful solvents and other chemicals. “It effectively replaced a 13-step solvent-based process used in the production of antibiotics, with a one-step enzyme that is clean, efficient and natural,” says Clements. “We’ve continued to evolve this process, which is now on its fifth generation.”
Finding forward-looking solutions to curb AMR
The company is also a founding member of the AMR Industry Alliance, a private-sector coalition that provides sustainable solutions to curb antimicrobial resistance. As such, Centrient is committed to complying with Predicted No-Effect Concentration (PNEC) discharge targets set by the Alliance. “PNEC is an industry standard,” says Clements. “We prioritise wastewater treatment at our manufacturing sites and ensure that we’re using the newest technology to manage AMR. Any water that leaves our facilities is fully compliant with these targets.”
In addition, the pharmaceutical company has worked with the British Standards Institute to develop an international industry standard for sustainable antibiotic manufacturing and, in 2023, piloted an independent AMR certification scheme. Earlier this year, they announced that they had been awarded the certification for their own site in Santa Perpetua, Spain. Plus, the company has invested in facilities in Europe and the Americas, ensuring it has diversified sourcing of key early-stage intermediate materials to protect antibiotic supply against stock end points.
Collective compliance with manufacturing standards
Going forward, Clements stresses the importance of collaboration between all stakeholders in the antibiotic space. “We need our competitors to comply with the same standards,” he says. “Otherwise, if practices generate AMR, it will reduce the effectiveness of our antibiotics. It’s important the industry works together to establish best practices and learn from each other. Centrient is one of the largest and among the last European manufacturers of antibiotics in Europe, ensuring we uphold the highest standards and set the industry benchmark.”